In the construction industry, Laminated Veneer Lumber (LVL) has emerged as a popular choice for enhancing building projects. LVL construction materials offer a range of benefits and are increasingly being used in various applications. This article explores the understanding, role, benefits, challenges, and future trends of LVL in modern construction.
Understanding LVL Construction Materials
Before delving into the specifics of lvl construction, let’s grasp the basics. Laminated Veneer Lumber is a type of engineered wood product made from several layers of thin wood veneer bonded together with adhesives. The layers are stacked parallel to each other, resulting in a strong and durable material.
The Basics of LVL Construction Materials
LVL offers exceptional structural performance due to its design. By aligning the wood fibers in the same direction across multiple layers, LVL maximizes strength and stiffness, making it an ideal choice for applications requiring load-bearing capabilities. Additionally, the manufacturing process ensures consistent quality, making LVL a reliable construction material.

Key Features of LVL Construction Materials
Beyond its structural attributes, LVL has several key features that enhance its appeal. Firstly, LVL is available in various sizes, allowing for flexibility in design and construction. This versatility enables architects and engineers to utilize LVL materials in a wide range of applications, from beams and columns to flooring systems.
Furthermore, LVL has excellent dimensional stability, meaning it resists warping, twisting, and shrinking to a greater degree when compared to solid wood. This stability ensures that LVL maintains its shape, even when subjected to changes in temperature and humidity, resulting in long-lasting and reliable structures.
Moreover, LVL is known for its environmental sustainability. The manufacturing process of LVL involves using fast-growing trees, such as pine and poplar, which are a renewable resource. This sustainable approach to sourcing raw materials makes LVL a popular choice for eco-conscious construction projects.
Additionally, LVL is highly resistant to moisture, making it suitable for applications in humid or wet environments. Its moisture resistance properties help prevent mold, mildew, and rot, ensuring the longevity of structures built with LVL materials. This feature is particularly advantageous in construction projects where exposure to moisture is a concern.
The Role of LVL in Modern Construction
LVL plays a vital role in both residential and commercial construction projects, offering unique advantages that cater to different needs.
LVL in Residential Construction
In residential construction, LVL finds wide application in various elements of the structure. It is commonly used in floor joists, roof trusses, and beams, providing a strong and stable framework to support the weight of the building. LVL’s dimensional stability also contributes to minimizing floor squeaks and reducing overall maintenance requirements.
Moreover, LVL is an eco-friendly choice for residential projects. It is often manufactured from sustainably sourced wood, minimizing environmental impact while providing a robust and sustainable alternative to traditional solid wood.
When it comes to architectural design, LVL offers flexibility and versatility. Its strength allows for open floor plans and larger spans, creating spacious and airy living spaces. Additionally, LVL’s uniformity in size and shape makes it easier for builders and architects to plan and execute their designs accurately.
LVL in Commercial Construction
In commercial construction, LVL materials offer exceptional load-bearing capabilities, making them suitable for larger-scale projects. From commercial buildings to bridges and warehouses, LVL is chosen for its ability to withstand heavy loads and resist bending. These applications benefit from LVL’s strength, durability, and ability to span longer distances compared to traditional wood or steel beams.
Furthermore, LVL’s fire-resistant properties make it a desirable material for commercial construction. With proper fire-retardant treatments, LVL can withstand high temperatures for extended periods, allowing for improved safety measures in buildings.
Another advantage of using LVL in commercial construction is its cost-effectiveness. LVL is often more affordable than other construction materials, such as steel or concrete, while still providing excellent structural performance. This cost-effectiveness makes LVL a preferred choice for projects with budget constraints.
Moreover, LVL’s sustainability credentials make it an attractive option for businesses aiming to meet environmental standards. By incorporating LVL into their construction projects, companies can demonstrate their commitment to sustainable practices and reduce their carbon footprint.
Benefits of Using LVL Construction Materials
The utilization of LVL construction materials brings forth a multitude of benefits for building projects.
When considering the durability and strength of LVL materials, it is essential to recognize the meticulous manufacturing process that goes into their production. Each layer of wood veneer is carefully selected and bonded together with adhesives under high pressure, resulting in a product that boasts exceptional strength and reliability. This attention to detail not only ensures the structural integrity of the material but also enhances its resistance to warping, twisting, and shrinking over time. Find more about pressure at https://www.princeton.edu/~asmits/Bicycle_web/pressure.html
Durability and Strength of LVL Materials
One of the primary advantages of LVL is its durability. The manufacturing process and engineered design result in a material that has consistent strength, minimizing the risk of structural failure. LVL’s ability to resist impact and hold heavy loads makes it suitable for demanding applications such as supporting floors, roofs, and walls.
Furthermore, LVL’s strength allows for significant design flexibility as it enables the construction of larger open spaces, reducing the need for intermediate columns or walls. This results in a more spacious and aesthetically pleasing environment.
Moreover, the sustainability aspects of LVL construction extend beyond its structural benefits. By choosing LVL materials for building projects, you are actively contributing to the preservation of our environment. The use of sustainable forestry practices ensures that the wood resources utilized in LVL production are responsibly sourced, promoting the long-term health of our forests and ecosystems.
Sustainability Aspects of LVL Construction
With growing environmental concerns, sustainable construction practices are becoming increasingly important. LVL addresses these concerns by utilizing renewable resources and reducing waste. By using thinner wood veneer layers, LVL allows efficient utilization of timber, ensuring the optimal use of each tree harvested.
Additionally, LVL’s long lifespan contributes to sustainability, as structures built with LVL materials require fewer replacements over time. This durability aspect reduces waste generation and promotes a more sustainable future in the construction industry.
Challenges and Solutions in Using LVL Materials
While LVL construction materials offer numerous benefits, certain challenges can arise during their implementation. However, these challenges are not insurmountable.
Understanding the intricacies of Laminated Veneer Lumber (LVL) materials is essential for successful construction projects. LVL is known for its strength, durability, and versatility, making it a popular choice for various structural applications. However, like any building material, LVL comes with its own set of challenges that builders and designers must address.
Common Issues with LVL Construction
One common challenge encountered with LVL is moisture-related swelling or shrinking. Changes in humidity levels can cause LVL to expand or contract, potentially affecting the structural integrity of the building. However, proper installation techniques, such as leaving gaps for expansion, can mitigate this issue.
Additionally, issues related to dimensional stability can arise if LVL materials are not stored or handled correctly. Improper storage conditions, such as exposure to extreme temperatures or moisture, can lead to warping or twisting of LVL components, impacting their performance in construction projects.
Another challenge is the susceptibility of LVL to fungal or insect attacks if not adequately protected. Applying preservatives and regular inspection can help prevent these issues and ensure the longevity of LVL construction materials. To learn more about fungal click here.
Overcoming LVL Construction Challenges
To overcome these challenges, it is crucial to follow proper installation guidelines and consult with professionals experienced in working with LVL materials. Implementing moisture control measures and utilizing appropriate treatments can mitigate potential issues and ensure optimal performance of LVL in construction projects.
Furthermore, incorporating design strategies that account for potential LVL movement due to environmental factors can help minimize the risk of structural issues over time. By considering factors such as building orientation, ventilation, and moisture barriers, builders can create more resilient structures that leverage the benefits of LVL materials while addressing their inherent challenges.
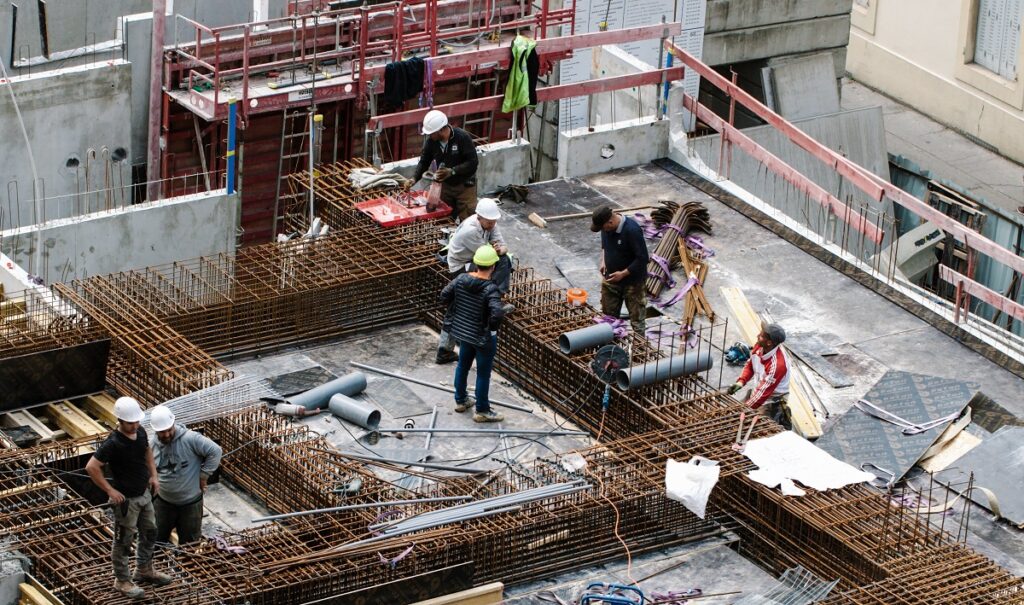
Future Trends in LVL Construction
LVL construction materials continue to evolve, driven by technological advancements and changing industry standards.
Technological Advancements in LVL Construction
With advancements in manufacturing techniques and material science, the performance and characteristics of LVL are continually improving. Emerging technologies, such as computer-controlled lamination processes, result in LVL products with enhanced strength and stiffness. These advancements enable designers and builders to push the boundaries of what can be achieved with LVL construction materials.
Moreover, research and development in the field of LVL construction are exploring innovative ways to enhance fire resistance and moisture protection in LVL products. By incorporating flame-retardant additives and moisture-resistant coatings, LVL materials are becoming more resilient in challenging environmental conditions, further expanding their applications in construction projects.
The Impact of LVL on Construction Industry Standards
LVL’s excellent performance and sustainability aspects have started to influence construction industry standards. As the demand for eco-friendly and durable materials grows, LVL is increasingly being incorporated into building codes and guidelines. This recognition underscores the significance of LVL in shaping the future of construction practices.
Furthermore, the versatility of LVL construction materials is leading to their integration into innovative architectural designs that prioritize both aesthetics and structural integrity. Architects and engineers are exploring new ways to utilize the strength and flexibility of LVL in creating unique building forms that were previously unattainable with traditional construction materials.
Overall, LVL construction materials offer numerous advantages that enhance building projects. From their structural performance and dimensional stability to their eco-friendliness and versatility, LVL is revolutionizing modern construction. While challenges exist, proper installation techniques and ongoing advancements ensure that LVL remains at the forefront of the construction industry, driving innovation and sustainability.
Learn about prices of lvl formwork at: Understanding Timber LVL Formwork Prices and Value